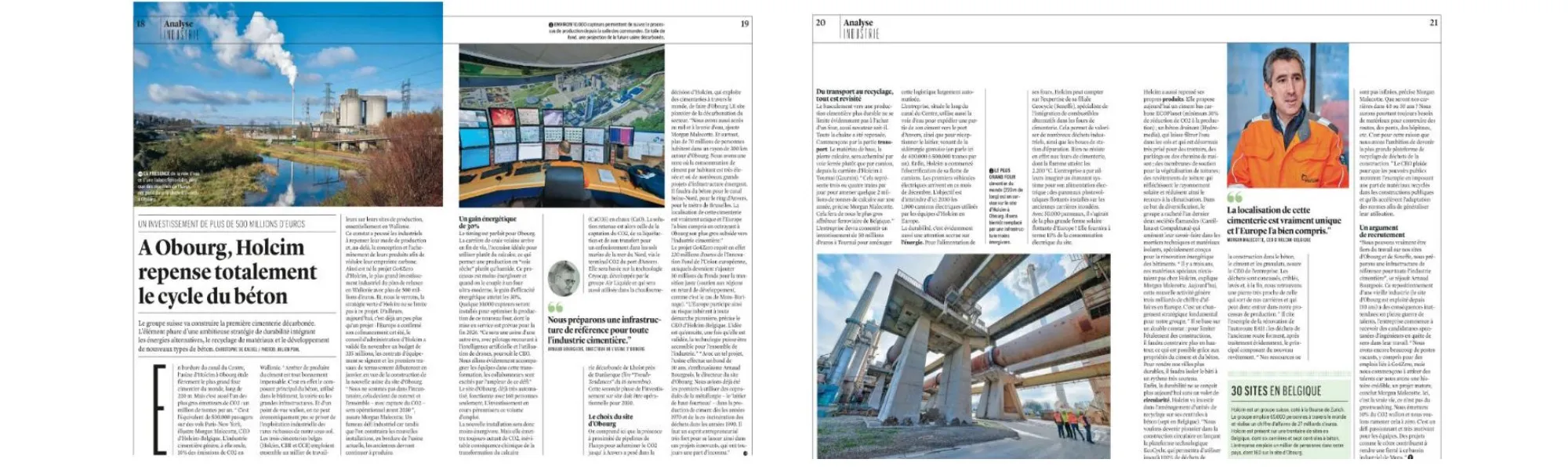
Un investissement de plus de 500 millions d’euros
A Obourg, Holcim repense totalement le cycle du béton
Le groupe suisse va construire la première cimenterie décarbonée. L’élément phare d’une ambitieuse stratégie de durabilité intégrant les énergies alternatives, le recyclage de matériaux et le développement de nouveaux types de béton.
En bordure du canal du Centre, l’usine d’Holcim à Obourg étale fièrement le plus grand four cimentier du monde, long de 220 m. Mais c’est aussi l’un des plus gros émetteurs de CO2 : un million de tonnes par an. “ C’est l’équivalent de 500.000 passagers sur des vols Paris-New York, illustre Morgan Malecotte, CEO d’Holcim-Belgique. L’industrie cimentière génère, à elle seule, 10% des émissions de CO2 en Wallonie. ” Arrêter de produire du ciment est tout bonnement impensable. C’est en effet le composant principal du béton, utilisé dans le bâtiment, la voirie ou les grandes infrastructures. Et d’un point de vue wallon, on ne peut économiquement pas se priver de l’exploitation industrielle des rares richesses de notre sous-sol. Les trois cimenteries belges (Holcim, CBR et CCB) emploient ensemble un millier de travailleurs sur leurs sites de production, essentiellement en Wallonie.Ce constat a poussé les industriels à repenser leur mode de production et, au-delà, la conception et l’acheminement de leurs produits afin de réduire leur empreinte carbone. Ainsi est né le projet Go4Zero d’Holcim, le plus grand investissement industriel du plan de relance en Wallonie avec plus de 500 millions d’euros. Et, nous le verrons, la stratégie verte d’Holcim ne se limite pas à ce projet. D’ailleurs, aujourd’hui, c’est déjà un peu plus qu’un projet : l’Europe a confirmé son cofinancement cet été, le conseil d’administration d’Holcim a validé fin novembre un budget de 335 millions, les contrats d’équipement se signent et les premiers travaux de terrassement débuteront en janvier, en vue de la construction de la nouvelle usine du site d’Obourg. “ Nous ne sommes pas dans l’incantatoire, cela devient du concret et l’ensemble – avec capture du CO2 – sera opérationnel avant 2030 ”, assure Morgan Malecotte. Un fameux défi industriel car tandis que l’on construira les nouvelles installations, en bordure de l’usine actuelle, les anciennes devront continuer à produire.
Un gain énergétique de 30%
Le timing est parfait pour Obourg. La carrière de craie voisine arrive en fin de vie, l’occasion idéale pour utiliser plutôt du calcaire, ce qui permet une production en “voie sèche” plutôt qu’humide. Ce processus est moins énergivore et quand on le couple à un four ultra-moderne, le gain d’efficacité énergétique atteint les 30%. Quelque 10.000 capteurs seront installés pour optimiser la production de ce nouveau four, dont la mise en service est prévue pour la fin 2026. “Ce sera une usine d’une autre ère, avec pilotage recourant à l’intelligence artificielle et l’utilisation de drones, poursuit le CEO. Nous allons évidemment accompagner les équipes dans cette transformation, les collaborateurs sont excités par l’ampleur de ce défi.” Le site d’Obourg, déjà très automatisé, fonctionne avec 160 personnes seulement. L’investissement en cours pérennisera ce volume d’emploi.La nouvelle installation sera donc moins énergivore. Mais elle émettra toujours autant de CO2, inévitable conséquence chimique de la transformation du calcaire (CaCO3) en chaux (CaO). La solution retenue est alors celle de la captation du CO2, de sa liquéfaction et de son transfert pour un enfouissement dans les sols marins de la mer du Nord, via le terminal CO2 du port d’Anvers. Elle sera basée sur la technologie Cryocap, développée par le groupe Air Liquide et qui sera aussi utilisée dans la chaufournerie décarbonée de Lhoist près de Dunkerque (lire “Trends- Tendances” du 16 novembre). Cette seconde phase de l’investissement sur site doit être opérationnelle pour 2030.
Le choix du site d’Obourg
On comprend ici que la présence à proximité de pipelines de Fluxys pour acheminer le CO2 jusqu’ à Anvers a pesé dans la décision d’Holcim, qui exploite des cimenteries à travers le monde, de faire d’Obourg LE site pionnier de la décarbonation du secteur. “Nous avons aussi accès au rail et à la voie d’eau, ajoute Morgan Malecotte. Et surtout, plus de 70 millions de personnes habitent dans un rayon de 300 km autour d’Obourg. Nous avons une zone où la consommation de ciment par habitant est très élevée et où de nombreux grands projets d’infrastructure émergent. Il faudra du béton pour le canal Seine-Nord, pour le ring d’Anvers, pour le métro de Bruxelles. La localisation de cette cimenterie est vraiment unique et l’Europe l’a bien compris en octroyant à Obourg son plus gros subside vers l’industrie cimentière.” Le projet Go4Zero reçoit en effet 230 millions d’euros de l’Innovation Fund de l’Union européenne, auxquels devraient s’ajouter 50 millions du Fonds pour la transition juste (soutien aux régions en retard de développement, comme c’est le cas de Mons-Borinage). “L’Europe participe ainsi au risque inhérent à toute démarche pionnière, précise le CEO d’Holcim-Belgique. L’idée est qu’ensuite, une fois qu’elle est validée, la technologie puisse être accessible pour l’ensemble de l’industrie. ” “ Avec un tel projet, l’usine effectue un bond de 50 ans, s’enthousiasme Arnaud Bourgeois, le directeur du site d’Obourg. Nous avions déjà été les premiers à utiliser des coproduits de la métallurgie – le ‘laitier de haut-fourneau’ – dans la production de ciment dès les années 1970 et de la co-incinération des déchets dans les années 1990. Il faut un esprit entrepreneurial très fort pour se lancer ainsi dans ces projets innovants, qui ont toujours une part d’inconnu.”
Du transport au recyclage, tout est revisité
Le basculement vers une production cimentière plus durable ne se limite évidemment pas à l’achat d’un four, aussi novateur soit-il. Toute la chaîne a été repensée. Commençons par la partie transport. Le matériau de base, la pierre calcaire, sera acheminé par voie ferrée plutôt que par camion, depuis la carrière d’Holcim à Tournai (Gaurain). “ Cela représente trois ou quatre trains par jour pour amener quelque 2 millions de tonnes de calcaire sur une année, précise Morgan Malecotte. Cela fera de nous le plus gros affréteur ferroviaire de Belgique. ” L’entreprise devra consentir un investissement de 50 millions d’euros à Tournai pour aménager cette logistique largement automatisée. L’entreprise, située le long du canal du Centre, utilise aussi la voie d’eau pour expédier une partie de son ciment vers le port d’Anvers, ainsi que pour réceptionner le laitier, venant de la sidérurgie gantoise (on parle ici de 400.000 à 500.000 tonnes par an). Enfin, Holcim a commencé l’électrification de sa flotte de camions. Les premiers véhicules électriques arrivent en ce mois de décembre. L’objectif est d’atteindre d’ici 2030 les 1.000 camions électriques utilisés par les équipes d’Holcim en Europe.La durabilité, c’est évidemment aussi une attention accrue sur l’énergie. Pour l’alimentation de ses fours, Holcim peut compter sur l’expertise de sa filiale Geocycle (Seneffe), spécialiste de l’intégration de combustibles alternatifs dans les fours de cimenterie. Cela permet de valoriser de nombreux déchets industriels, ainsi que les boues de station d’épuration. Rien ne résiste en effet aux fours de cimenterie, dont la flamme atteint les 2.200 °C. L’entreprise a par ailleurs imaginé un étonnant système pour son alimentation électrique : des panneaux photovoltaïques flottants installés sur les anciennes carrières inondées. Avec 50.000 panneaux, il s’agirait de la plus grande ferme solaire flottante d’Europe ! Elle fournira à terme 15% de la consommation électrique du site. Holcim a aussi repensé ses propres produits. Elle propose aujourd’hui un ciment bas carbone ECOPlanet (minimum 30% de réduction de CO2 à la production) ; un béton drainant (Hydromedia), qui laisse filtrer l’eau dans les sols et qui est désormais très prisé pour des trottoirs, des parkings ou des chemins de maison ; des membranes de soutien pour la végétalisation de toitures ; des revêtements de toiture qui réfléchissent le rayonnement solaire et réduisent ainsi le recours à la climatisation. Dans ce but de diversification, le groupe a racheté l’an dernier deux sociétés flamandes (Cantillana et Compaktuna) qui amènent leur savoir-faire dans les mortiers techniques et matériaux isolants, spécialement conçus pour la rénovation énergétique des bâtiments. “ Il y a trois ans, ces matériaux spéciaux n’existaient pas chez Holcim, explique Morgan Malecotte. Aujourd’hui, cette nouvelle activité génère trois milliards de chiffre d’affaires en Europe. C’est un changement stratégique fondamental pour notre groupe. ” Il se base sur un double constat : pour limiter l’étalement des constructions, il faudra construire plus en hauteur, ce qui est possible grâce aux propriétés du ciment et du béton. Pour rendre nos villes plus durables, il faudra isoler le bâti à un rythme très soutenu.Enfin, la durabilité ne se conçoit plus aujourd’hui sans un volet de circularité. Holcim va investir dans l’aménagement d’unités de recyclage sur ses centrales à béton (sept en Belgique). “Nous voulons devenir pionnier dans la construction circulaire en lançant la plateforme technologique EcoCycle, qui permettra d’utiliser jusqu’à 100% de déchets de la construction dans le béton, le ciment et les granulats, assure le CEO de l’entreprise. Les déchets sont concassés, criblés, lavés et, à la fin, nous retrouvons une pierre très proche de celle qui sort de nos carrières et qui peut donc entrer dans notre processus de production. ” Il cite l’exemple de la rénovation de l’autoroute E411 : les déchets de l’ancienne route forment, après traitement évidemment, le principal composant du nouveau revêtement. “ Nos ressources ne sont pas infinies, précise Morgan Malecotte. Que seront nos carrières dans 40 ou 50 ans ? Nous aurons pourtant toujours besoin de matériaux pour construire des routes, des ponts, des hôpitaux, etc. C’est pour cette raison que nous avons l’ambition de devenir la plus grande plateforme de recyclage de déchets de la construction. ” Le CEO plaide pour que les pouvoirs publics montrent l’exemple en imposant une part de matériaux recyclés dans les constructions publiques et qu’ils accélèrent l’adaptation des normes afin de généraliser leur utilisation.
Un argument de recrutement
“Nous pouvons vraiment être fiers du travail sur nos sites d’Obourg et de Seneffe, nous préparons une infrastructure de référence pour toute l’industrie cimentière”, se réjouit Arnaud Bourgeois. Ce repositionnement d’une vieille industrie (le site d’Obourg est exploité depuis 110 ans) a des conséquences inattendues: en pleine guerre de talents, l’entreprise commence à recevoir des candidatures spontanées d’ingénieurs en quête de sens dans leur travail. “ Nous avons encore beaucoup de postes vacants, y compris pour des emplois liés à Go4Zero, mais nous commençons à attirer des talents car nous avons une histoire crédible, un projet mature, conclut Morgan Malecotte. Ici, c’est la vraie vie, ce n’est pas du greenwashing. Nous émettons 10% du CO2 wallon et nous voulons ramener cela à zéro. C’est un défi passionnant et très motivant pour les équipes. Des projets comme le nôtre contribuent à rendre une fierté à ce bassin industriel de Mons. ” LA PRéSENCE de la voie d’eau et d’une liaison ferroviaire, ainsi que des pipelines de Fluxys, ont pesé dans le choix d’investir à Obourg. LE PLUS GRAND FOUR cimentier du monde (220 m de long) est en service sur le site d’Holcim à Obourg. Il sera bientôt remplacé par une infrastructure moins énergivore. Nous préparons une infrastructure de référence pour toute l’industrie cimentière.” Arnaud Bourgeois, directeur de l’usine d’Obourg.
30 sites en Belgique
Holcim est un groupe suisse, coté à la Bourse de Zurich. Le groupe emploie 65.000 personnes à travers le monde et réalise un chiffre d’affaires de 27 milliards d’euros. Holcim est présent sur une trentaine de sites en Belgique, dont six carrières et sept centrales à béton. L’entreprise emploie un millier de personnes dans notre pays, dont 160 sur le site d’Obourg.